Flexographic printing for Aseptic Liquid Package
8/10 colors
Print width: 1270 mm
Max print speed: 400 m/min
Print repeat: 370-940 mm
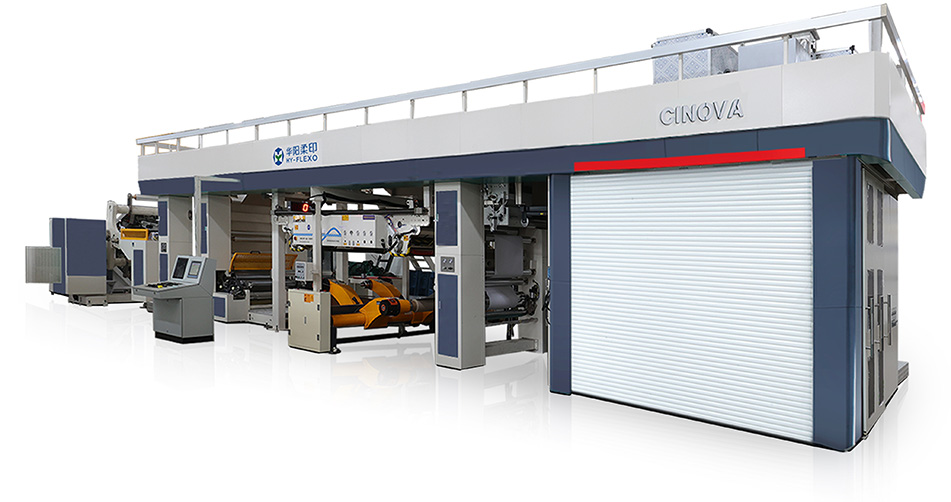
The CINOVA-Liquid CI Flexo Press is designed for printing paper for aseptic liquid package. Reaching a printing speed of 400m/min, it is featured for its’ high automation, high productivity, user-friendly operation, and smart production management.
Specifications
Print colors | 8 / 10 colors |
Substrate | Paper 80-350 gsm |
Print width | 1270 mm (50.0 in) |
Print repeat | 370-940 mm (14.5-37.0 in) |
Max print speed | 400 m/min (1312 ft/min) |
Max. unwind/rewind diameter | Φ1500 mm (59.0 in) |
Applications
Features
- Control and servo drive system
- Cantilever structure for anilox sleeve and print sleeve
- Central drum with constant temperature control system
- Close chamber doctor blade, reliable and easy for change
- Non-stop roll change (unload / load platform)
- Job management system
- Easy operation pre-register system
- Pressure servo control and pre-adjustment system
- Adjustable drying system
- Ink control and auto wash system
- Volatile gas recovery device
- System fault monitoring system
- Remote diagnosis and maintenance system
Advantages
Superior print quality
- Robust cast iron frame guarantees the machine with high stability and accuracy
- Central drum direct drive technology guarantees the high transmission precision
- Servo motor guarantees excellent print pressure and registration control
- Reliable ink chamber system guarantees best ink transfer
- Inline defect detection system
Easy Operation
- User-friendly HMI
- One-touch machine setup
- Automatic print pressure and registration control
- Automatic ink washing system
- Automatic roll lifting system
- Intelligent production management system
- 24/7 remote assistance for troubleshooting and maintenance
Quick Job Change
- One-touch machine setup
- Cantilever structure for quick sleeve changeover
- Quick pressure adjustment and pre-registration
- Quick ink washing system
- Job memory for history jobs
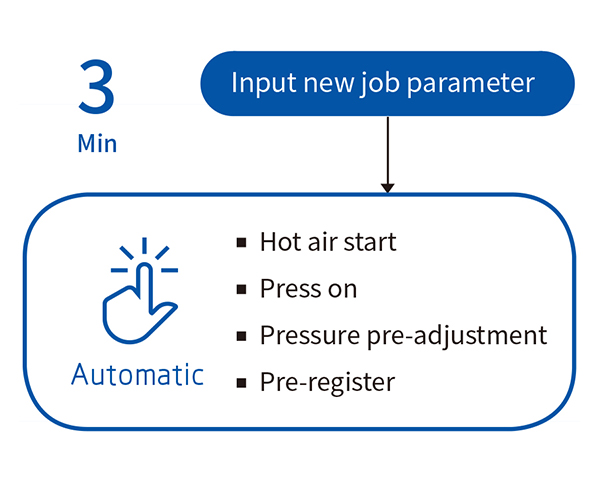
One key setup
By means of pressure pre-set and pre-register, the setup time has been reduced from 25 min to 3 min, which shortness the preparation time and effectively lowers the cost.
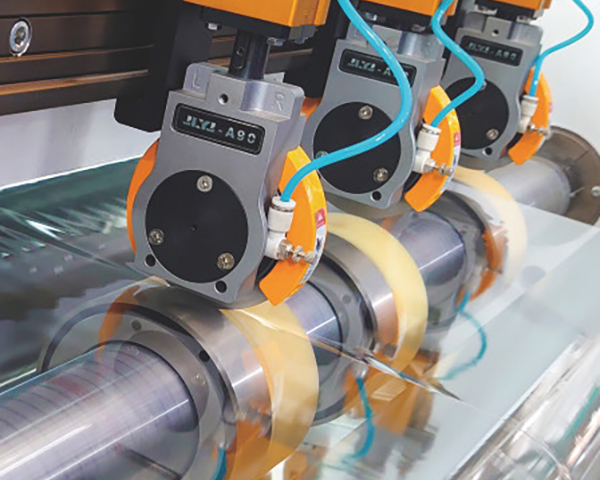
Automatic pressure compensation
The function enables the print pressure to be adjusted automatically when machine speed changes, thus avoiding the register tolerance and color difference caused by pressure changes. The function helps the machine to have stable print when machine speed changes.

Speed selft-adaption control system
By comparing the torque value and adjusting the anilox motor speed, the system will reduce the torque difference and eliminate the ink bar caused by a bit heavy pressure printing.
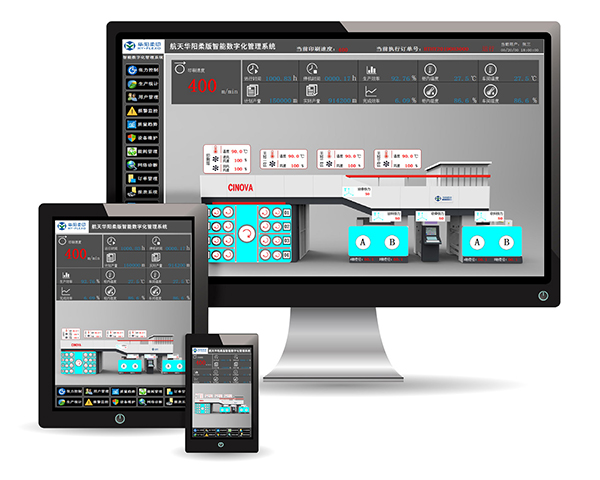
Intelligent Production Management System
The system is developed to improve production efficiency and monitor the production process real time. By using a smart phone or a computer, management team is able to monitor at real time the machine production status and workshop site status. The system helps factories reduce the down time and operation cost.
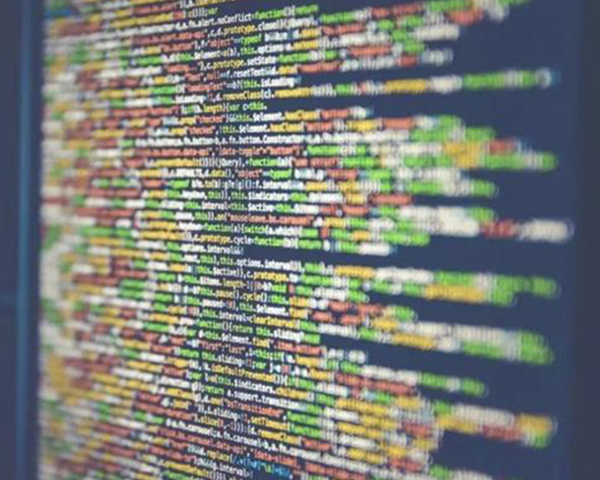
Job memory & one-key retrieval
The function is intended for storing technical parameters for 99 jobs. The function enables the history job parameters to be retrieved easily. The print decks can move to set position and start printing without any further setting. When the machine stops, the last position of print sleeve will be memorized. When the machine starts again, it will start working from the same position.

Print length measuring
The system will measure the print length real time and send the feedback to tension system. The system will make adjustment automatically to ensure invariable print length, thus reducing the defects rate.